The Vital Role of Prototyping in Custom Electromagnetic Solutions
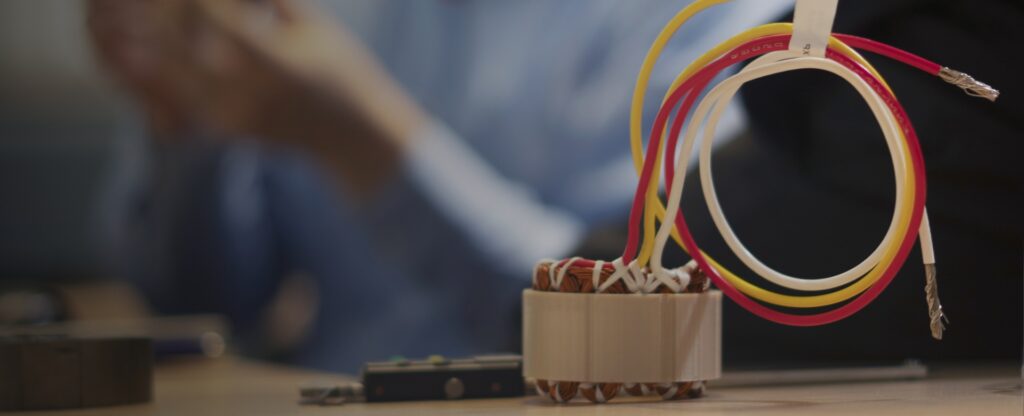
Introduction
In the fast-paced world of engineering and technology, the ability to quickly and efficiently prototype new designs is a game-changer. Prototyping plays a critical role in the development of custom electromagnetic solutions, especially in industries where precision and reliability are paramount. From aerospace to defense, and advanced air mobility to energy sectors, the significance of prototyping cannot be overstated. At Windings Inc., we recognize this importance and have tailored our Rapid Prototyping and Customization (RPC) services to meet the highest standards of performance and reliability.
The Importance of Prototyping in the Motor Industry
Prototyping is a crucial step in the product development process. It allows engineers to test and refine their designs before committing to full-scale production. This iterative process helps identify potential issues early on, reducing the risk of costly errors and ensuring that the final product meets all specifications. In the motor industry, where components are often subjected to extreme conditions, prototyping ensures that motors and related parts can withstand operational stresses and deliver reliable performance.
Key Benefits of Prototyping
- Design Validation: Prototyping allows for the physical validation of design concepts. Engineers can test the fit, form, and function of their designs, making necessary adjustments before moving to the next stage. This is particularly important in the motor industry, where precise dimensions and mechanical properties are critical for optimal performance.
- Performance Testing: By creating prototypes, engineers can conduct performance tests to ensure that the product meets the required standards. This includes testing for strength, durability, efficiency, and other critical parameters. For instance, motors used in aerospace applications must be tested for high-altitude performance and resistance to temperature variations.
- Cost Reduction: Identifying and resolving design flaws during the prototyping phase can significantly reduce production costs. It prevents the need for expensive modifications or recalls after the product has been manufactured. This is especially true for custom motors designed for specific applications, where any post-production changes can be costly and time-consuming.
- Accelerated Time-to-Market: Prototyping speeds up the development process by allowing for rapid iterations and refinements. This can lead to faster time-to-market, giving companies a competitive edge. In industries such as defense, where technology needs to be deployed quickly and efficiently, this can be a crucial advantage.
Prototyping in Critical Applications
The motor industry serves various critical applications, each with its own set of stringent requirements. Here are some examples:
- Aerospace: In aerospace, electric motors are used in a variety of applications, from actuating control surfaces to driving fuel pumps. These motors must operate reliably under extreme conditions, including high altitudes, temperature fluctuations, and intense vibrations. Prototyping allows aerospace engineers to test these motors in simulated environments, ensuring they meet all operational requirements before being deployed in actual aircraft​​​​.
- Defense: Defense applications often require custom motors designed to meet specific performance criteria. For instance, motors used in missile fin actuators or unmanned aerial vehicles (UAVs) must be lightweight, powerful, and highly reliable. Prototyping enables defense contractors to test these motors in controlled conditions, ensuring they can withstand the rigors of battlefield operations​​​​.
- Advanced Air Mobility: The emerging field of advanced air mobility (AAM) includes electric vertical takeoff and landing (eVTOL) aircraft, which rely heavily on electric motors. These motors must provide high torque output while maintaining critical magnet retention during high-speed rotations. Prototyping allows engineers to explore different design configurations and materials, ensuring the final product delivers optimal performance​​.
- Energy: In the energy sector, electric motors are used in applications such as downhole drilling and power generation. These motors must operate reliably in harsh environments, including high temperatures and pressures. Prototyping helps energy companies test and refine their motor designs, ensuring they can withstand these conditions and deliver consistent performance​​​​.
Windings Inc. Prototyping Capabilities
At Windings Inc., prototyping is one of our core competencies. We offer a range of prototyping services designed to meet the needs of our clients in various industries, including aerospace, defense, advanced air mobility, and energy.
- Rapid Prototyping: Our rapid prototyping capabilities enable us to quickly build and test components, allowing for multiple design iterations in a short period. This is particularly valuable in projects with tight schedules. Rapid prototyping accelerates the development cycle, allowing engineers to refine designs quickly and efficiently.
- 3D Printing: We utilize 3D printing technology to create precise prototypes of components. This allows for quick testing and validation of design concepts, ensuring that they meet all specifications. 3D printing is particularly useful for creating complex geometries that would be difficult or expensive to produce using traditional manufacturing methods.
- Testing and Validation: We have a range of testing facilities to validate the performance of our prototypes. This includes dynamometer test stands, speed-torque testing, and thermal stress testing. Comprehensive testing ensures that prototypes perform as expected under real-world conditions, providing valuable data for further refinement.
Key Needs for Prototyping
- Complexity of Designs: Modern electromagnetic solutions often involve complex designs that must meet precise specifications. Prototyping helps in understanding the real-world behavior of these designs, ensuring they meet the required performance standards.
- Critical Performance Requirements: Industries like aerospace and defense have stringent performance requirements. Prototyping allows for thorough testing under simulated conditions, ensuring that the final product can withstand the rigors of its operational environment.
- Innovation and Customization: Prototyping fosters innovation by allowing engineers to experiment with new ideas and materials. It also supports customization, enabling the development of tailored solutions for specific applications.
Steps in the Prototyping Process
- Conceptualization: This initial stage involves brainstorming and conceptualizing the design. Engineers create sketches, CAD models, and simulations to visualize the product.
- Design and Simulation: Using advanced design tools like SolidWorks and MotorCAD, engineers develop detailed models of the prototype. These models are then subjected to simulations to predict their performance under various conditions.
- Material Selection: Choosing the right materials is crucial for the success of the prototype. Factors such as strength, thermal conductivity, and electrical resistivity are considered during this step.
- Fabrication: Once the design is finalized, the prototype is fabricated using methods such as 3D printing, CNC machining, and custom winding. This stage may involve multiple iterations to refine the design.
- Testing and Validation: The fabricated prototype undergoes rigorous testing to validate its performance. Tests may include dynamometer testing, thermal stress testing, and speed-torque testing. Data from these tests is used to make further refinements to the design.
- Review and Optimization: Based on the testing results, engineers review the design and make necessary optimizations. This iterative process continues until the prototype meets all performance criteria.
Benefits of Prototyping
- Design Validation:
Prototyping allows for the physical validation of design concepts. Engineers can test the fit, form, and function of their designs, making necessary adjustments before moving to the next stage. This is particularly important in the motor industry, where precise dimensions and mechanical properties are critical for optimal performance. - Performance Testing:
By creating prototypes, engineers can conduct performance tests to ensure that the product meets the required standards. This includes testing for strength, durability, efficiency, and other critical parameters. For instance, motors used in aerospace applications must be tested for high-altitude performance and resistance to temperature variations. - Cost Reduction:
Identifying and resolving design flaws during the prototyping phase can significantly reduce production costs. It prevents the need for expensive modifications or recalls after the product has been manufactured. This is especially true for custom motors designed for specific applications, where any post-production changes can be costly and time-consuming. - Accelerated Time-to-Market:
Prototyping speeds up the development process by allowing for rapid iterations and refinements. This can lead to faster time-to-market, giving companies a competitive edge. In industries such as defense, where technology needs to be deployed quickly and efficiently, this can be a crucial advantage.
Drawbacks of Prototyping
- Initial Costs: Prototyping can be expensive, particularly when using advanced materials and fabrication techniques. However, these costs are often offset by the savings achieved through early detection of design flaws.
- Time-Consuming: The iterative nature of prototyping can be time-consuming. Each design iteration requires fabrication and testing, which can extend the development timeline. However, the time invested in prototyping is typically recouped through faster time-to-market and reduced post-production modifications.
- Resource Intensive: Prototyping requires specialized equipment and skilled personnel. This can strain resources, especially for smaller companies. Partnering with a company like Windings Inc., which has extensive prototyping capabilities, can help mitigate this issue.
Future Trends in Prototyping for the Motor Industry
The motor industry continues to evolve, driven by advancements in materials science, manufacturing technologies, and simulation tools. Future trends in prototyping include:
- Digital Twin Technology: Digital twins are virtual replicas of physical components. They allow engineers to simulate and analyze the performance of motors in real-time, providing valuable insights for design optimization. Digital twin technology can significantly reduce the time and cost associated with physical prototyping.
- Advanced Materials: The use of advanced materials, such as carbon fiber composites and high-temperature alloys, is expanding in the motor industry. These materials offer superior performance characteristics but require specialized prototyping techniques to fully leverage their benefits.
- Automation and AI: Automation and artificial intelligence are playing an increasingly important role in prototyping. Automated manufacturing processes and AI-driven design tools can accelerate prototyping, reduce errors, and improve the overall quality of prototypes.
Considerations for Prototyping Electric Motors
Prototyping electric motors involves a range of critical considerations to ensure that the final product meets stringent performance and reliability standards. These considerations encompass design validation, material selection, testing methodologies, and manufacturing processes.
- Design Complexity: Electric motors, especially those used in high-performance applications, often have intricate designs with precise specifications. Engineers must consider the complexity of the design and ensure that the prototype accurately reflects the intended functionality. This includes detailed CAD modeling and simulations to predict performance characteristics and identify potential issues early in the development process.
- Material Selection:
Choosing the right materials is paramount for the success of an electric motor prototype. Factors such as magnetic properties, thermal conductivity, electrical resistivity, and mechanical strength must be considered. Advanced materials, such as high-temperature alloys and carbon fiber composites, may be required to meet specific application needs. Engineers must balance performance requirements with material costs and availability. - Manufacturing Techniques: Prototyping electric motors often involves specialized manufacturing techniques such as 3D printing, CNC machining, and custom winding. Each technique has its advantages and limitations. For instance, 3D printing is excellent for creating complex geometries but may not always meet the strength requirements of certain components. CNC machining provides high precision but can be time-consuming and expensive. The choice of manufacturing technique depends on the specific requirements of the prototype and the intended application.
- Thermal Management: Electric motors generate heat during operation, and effective thermal management is crucial to ensure reliability and performance. Prototypes must be tested for thermal performance, including heat dissipation and insulation properties. Engineers need to consider the operating environment and ensure that the motor can maintain optimal performance without overheating.
- Magnetic Properties: The performance of electric motors is heavily influenced by the magnetic properties of the materials used in the rotor and stator. Prototyping allows engineers to experiment with different magnetic materials and configurations to achieve the desired torque, efficiency, and power density. Ensuring that the prototype meets the required magnetic specifications is essential for the motor’s overall performance.
- Testing and Validation: Comprehensive testing is a critical component of the prototyping process. Prototypes must undergo rigorous testing to validate their performance under real-world conditions. This includes dynamometer testing to measure speed-torque characteristics, thermal testing to assess heat management, and endurance testing to ensure long-term reliability. Testing provides valuable data that can be used to refine the design and address any shortcomings.
- Iterative Refinement: Prototyping is an iterative process. Initial prototypes may reveal design flaws or performance issues that need to be addressed. Engineers must be prepared to make multiple iterations of the prototype, each time refining the design based on testing feedback. This iterative approach helps ensure that the final product meets all performance and reliability criteria.
- Cost and Time Constraints: While prototyping is essential, it can also be resource-intensive. Engineers must consider the cost and time constraints associated with developing prototypes. Balancing the need for thorough testing and refinement with project budgets and timelines is a crucial aspect of the prototyping process. Efficient project management and leveraging advanced tools and techniques can help mitigate these constraints.
Conclusion
Prototyping is an indispensable part of the engineering process, particularly in the development of custom electromagnetic solutions. In critical applications across aerospace, defense, advanced air mobility, and energy sectors, prototyping ensures that motors and related components meet the highest standards of performance and reliability. At Windings Inc., our prototyping services are designed to help our clients achieve their goals efficiently and effectively. By leveraging our expertise and advanced capabilities, we ensure that our clients receive the highest quality products that meet their specific needs.
For more information on our prototyping services and how we can help with your next project, please contact us at sales@www.windings.com or visit our website at www.windings.com.