The Importance of Rotor Balancing in Electromagnetic Solutions
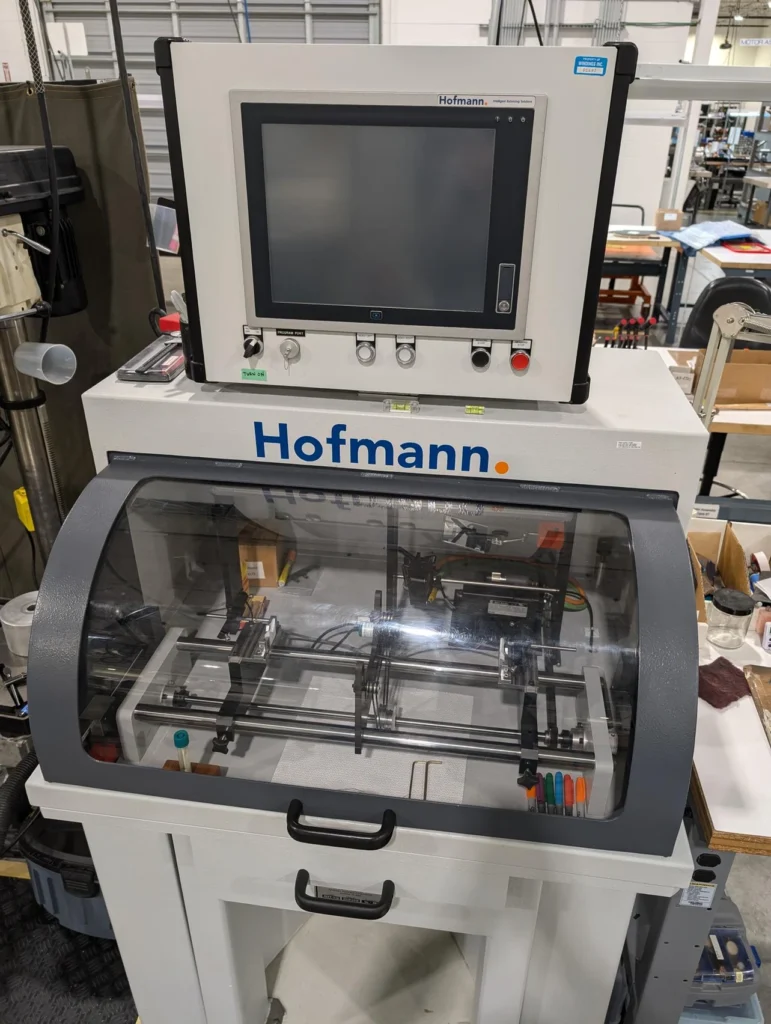
Introduction
Rotor balancing is a critical aspect of manufacturing high-performance electric motors. Ensuring that the rotor is balanced minimizes vibration, reduces wear on bearings, and improves the overall efficiency and longevity of the motor. At Windings, Inc., we recognize the importance of precision in rotor balancing, especially given our focus on custom electric motors and related components for critical applications in aerospace, defense, advanced air mobility, and energy sectors.
Why Rotor Balancing Matters
Rotor imbalance can cause significant issues in motor performance. An unbalanced rotor can lead to several operational challenges, including:
- Increased Vibration: This can cause noise, discomfort, and even damage to the motor and its surroundings. Vibration is a primary concern because it can lead to resonance, which amplifies the vibrations, potentially causing structural failures in the motor or its mounting.
- Bearing Wear: Imbalance leads to uneven load distribution on the bearings, reducing their lifespan and increasing the risk of failure. Bearings are critical components in electric motors, and their premature failure can lead to costly repairs and downtime.
- Reduced Efficiency: Vibration and friction from imbalance can reduce the motor’s efficiency, leading to higher energy consumption and operational costs. In applications where energy efficiency is critical, such as in electric vehicles or aerospace, this can significantly impact performance.
- Operational Reliability: For mission-critical applications, any downtime or failure due to rotor imbalance can be costly and dangerous. In industries like aerospace and defense, the reliability of every component, including the motor, is paramount.
The Balancing Process
At Windings, we employ state-of-the-art technology and meticulous processes to ensure our rotors are perfectly balanced. Our balancing process includes:
- Initial Design and Simulation
Using advanced design tools like SolidWorks and MotorCAD, we simulate the rotor’s performance to identify potential imbalance issues before manufacturing begins. These simulations help us understand how the rotor will behave under different operating conditions and allow us to make necessary adjustments to the design early in the development process. - Precision Manufacturing
During production, we ensure that each component is manufactured to exact specifications. This includes custom machining of rotors and other components to achieve the desired balance. Precision manufacturing involves maintaining tight tolerances and using high-quality materials to ensure consistency and reliability. - Dynamic Balancing
We perform dynamic balancing on each rotor, using high-precision balancing machines to detect and correct any imbalance. Dynamic balancing involves spinning the rotor and measuring the vibration caused by imbalance. We then add or remove material to correct the imbalance, ensuring that the rotor operates smoothly at all speeds.
Benefits of Balanced Rotors
Balanced rotors offer numerous advantages, particularly for high-performance and mission-critical applications:
- Extended Motor Life
By reducing vibration and bearing wear, balanced rotors extend the overall lifespan of the motor. This is especially important in applications where motors are difficult to access and replace, such as in aerospace and oil and gas drilling. - Improved Performance
A well-balanced rotor ensures smoother operation, higher efficiency, and better energy utilization. This leads to better overall performance of the motor and can enhance the performance of the entire system in which the motor is integrated. - Reliability in Harsh Conditions
For applications in extreme environments, such as aerospace and oil and gas, balanced rotors provide the reliability needed to maintain continuous operation without failure. This is critical for mission-critical applications where failure is not an option. - Cost Savings
Reduced maintenance and downtime translate to significant cost savings over the motor’s operational life. By extending the lifespan of the motor and reducing the need for repairs, balanced rotors help lower the total cost of ownership.
Rotor Balancing Techniques
To achieve optimal balance, several techniques are employed:
- Material Removal
Small amounts of material are removed from the rotor at specific locations to correct imbalance. This technique requires precision and is often performed using CNC machines that can remove material accurately and consistently. - Weight Addition
Weights are added to precise locations on the rotor to counteract imbalance. This technique is used when removing material is not feasible or when additional mass is needed to achieve balance. - Precision Machining
Advanced machining techniques ensure that all components are manufactured to exact specifications, minimizing initial imbalance. This involves using high-precision lathes, mills, and other machining equipment to produce components with tight tolerances.
The Science Behind Rotor Balancing
Rotor balancing is grounded in principles of physics and engineering. The goal is to ensure that the center of mass of the rotor coincides with its geometric center. Any deviation from this can cause centrifugal forces during rotation, leading to vibration and other issues.
Centrifugal Forces and Imbalance
When a rotor is imbalanced, the center of mass does not align with the axis of rotation. As the rotor spins, the off-center mass creates a centrifugal force that tries to move the rotor away from its axis. This force increases with the square of the rotational speed, making imbalance more problematic at higher speeds.
Vibration Analysis
Vibration analysis is a key part of the balancing process. By measuring the vibration of the rotor as it spins, we can determine the magnitude and phase of the imbalance. This information allows us to make precise adjustments to the rotor to correct the imbalance.
Advanced Tools and Techniques
At Windings, we utilize a range of advanced tools and techniques to achieve precise rotor balancing:
- Finite Element Analysis (FEA)
FEA is a computational technique used to simulate how a rotor will behave under different conditions. By modeling the rotor in a virtual environment, we can predict areas of potential imbalance and make necessary design adjustments before manufacturing. - Laser Balancing
Laser balancing involves using laser technology to measure the rotor’s dimensions and alignment with high precision. This technique helps us achieve tight tolerances and ensures that the rotor is perfectly balanced. - High-Speed Balancing
High-speed balancing machines spin the rotor at its operating speed to measure and correct imbalance. This is crucial for applications where the rotor operates at high speeds, as imbalance effects are more pronounced at these speeds.
The Role of Materials in Rotor Balancing
The choice of materials plays a significant role in rotor balancing. Different materials have different densities, which affects their balance. Additionally, the manufacturing process for each material can introduce imbalances.
Material Properties
Key properties of materials used in rotor manufacturing include:
- Density: Higher density materials can be more challenging to balance but offer better structural integrity.
- Thermal Expansion: Materials that expand significantly with temperature changes can cause imbalance during operation.
- Machinability: Some materials are easier to machine to tight tolerances, which aids in achieving balance.
Advanced Materials
Windings, Inc. uses advanced materials such as carbon fiber and specialized alloys to achieve optimal balance and performance in our rotors. Carbon fiber, for example, offers high strength-to-weight ratios and low thermal expansion, making it ideal for high-speed applications.
Applications of Balanced Rotors
Balanced rotors are essential in a variety of applications, each with unique requirements:
Aerospace
In aerospace, motors must operate reliably under extreme conditions, including high speeds, temperature fluctuations, and varying loads. Balanced rotors ensure that the motors can perform consistently and reliably in these demanding environments.
Defense
Defense applications require motors that can withstand harsh conditions and provide reliable performance over long periods. Balanced rotors help achieve these goals by reducing wear and increasing the lifespan of the motors.
Advanced Air Mobility
Emerging sectors like advanced air mobility demand high-performance motors that can operate efficiently and reliably. Balanced rotors are crucial in ensuring these motors meet the performance and reliability standards required for applications like electric vertical takeoff and landing (eVTOL) aircraft.
Energy
In the energy sector, particularly in oil and gas, balanced rotors are essential for motors used in downhole tools and other harsh environments. These motors must operate reliably under high temperatures and pressures, making balance critical for performance and longevity.
Continuous Improvement and Innovation
At Windings, Inc., we are committed to continuous improvement and innovation in rotor balancing. We invest in research and development to explore new materials, technologies, and techniques that can further enhance the balance and performance of our rotors.
Research and Development
Our R&D team works closely with industry partners and academic institutions to stay at the forefront of rotor balancing technology. This collaboration allows us to incorporate the latest advancements into our products and processes, ensuring that we continue to deliver high-quality, high-performance motors to our customers.
Customer Feedback
We value feedback from our customers and use it to drive improvements in our rotor balancing processes. By understanding the challenges and requirements of our customers, we can tailor our solutions to meet their specific needs and ensure the highest levels of satisfaction.
Conclusion
Rotor balancing is an essential aspect of producing high-quality electric motors. At Windings, Inc., we are committed to ensuring that every rotor we manufacture meets the highest standards of balance and performance. By leveraging advanced design tools, precision manufacturing, and dynamic balancing techniques, we deliver motors that excel in even the most demanding applications.
For more information on our rotor balancing services and how we can help optimize your motor designs, contact us at sales@www.windings.com or visit our website at Windings Inc.