Nearshoring: A Strategic Move to Strengthen Supply Chains in Manufacturing
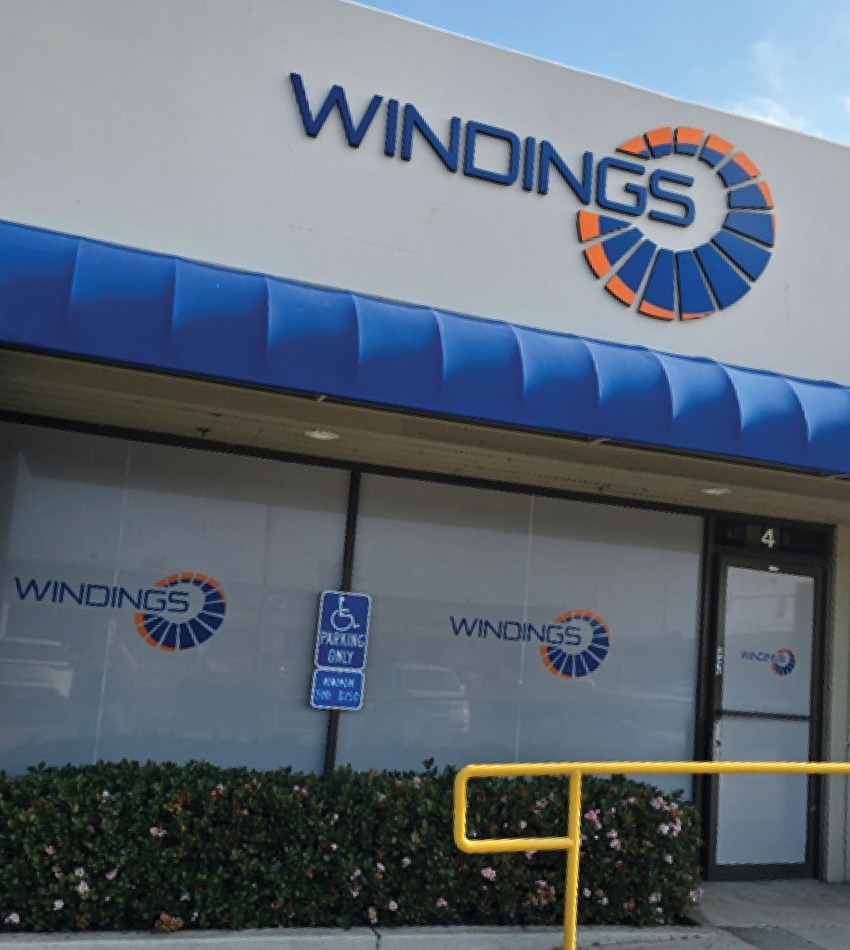
In recent years, global manufacturing has faced numerous challenges, from fluctuating tariffs and geopolitical tensions to supply chain disruptions caused by natural disasters and pandemics. As businesses seek to navigate these complexities, nearshoring—relocating manufacturing operations within the same region—has become a key strategy for improving operational resilience and reducing costs.
This blog explores the advantages of nearshoring, particularly in industries requiring precision engineering and timely production, such as aerospace, defense, and energy. We will also discuss how Windings Inc.’s strategic acquisitions of new facilities, including one in Baja California, Mexico, demonstrate the growing importance of nearshoring in maintaining supply chain agility and enhancing manufacturing capabilities.
Understanding Nearshoring: What Is It and Why Is It Important?
Nearshoring refers to the practice of relocating manufacturing operations to nearby countries or regions, often within the same time zone or geographical area. For companies based in the United States, nearshoring typically involves moving production from distant offshore locations, such as China or Southeast Asia, to countries in North America, such as Mexico or Canada.
This shift is driven by a need for greater control over supply chains, reduced lead times, and the ability to respond more quickly to market demands. Nearshoring also offers a solution to rising labor costs in traditional offshoring locations and provides a buffer against global disruptions like those experienced during the COVID-19 pandemic.
Key Advantages of Nearshoring
- Reduced Lead Times and Improved Responsiveness
One of the most significant advantages of nearshoring is the reduction in lead times. With production facilities closer to home, manufacturers can reduce transit times, allowing for faster delivery of products to customers. In industries such as aerospace, defense, and automotive, where timing is critical, nearshoring ensures that companies can meet tight deadlines and quickly adapt to changes in demand.
For example, aerospace manufacturers often need highly specialized components on short notice to meet production schedules. By nearshoring production, companies can shorten the supply chain and enhance their ability to fulfill orders on time without the lengthy delays that can arise from overseas shipping. - Cost Efficiency Through Reduced Transportation Expenses
Shipping costs can account for a significant portion of a company’s operational expenses, especially when goods are transported over long distances. Nearshoring reduces these costs by minimizing the distance between production facilities and their target markets.
In addition to saving on freight costs, companies can also avoid the financial burden of tariffs, customs fees, and duties that often come with offshore manufacturing. With nearshoring, particularly when sourcing from Mexico or Canada, manufacturers can take advantage of trade agreements like the United States-Mexico-Canada Agreement (USMCA), further reducing costs associated with international trade. - Enhanced Supply Chain Resilience
The COVID-19 pandemic underscored the fragility of global supply chains. Disruptions to manufacturing in Asia, combined with port backlogs and transportation bottlenecks, left many companies scrambling to secure parts and materials. Nearshoring mitigates these risks by keeping production within closer geographical proximity, allowing for faster resolution of supply chain issues.
By reducing reliance on distant suppliers, companies can strengthen their supply chain resilience. Nearshoring also allows for better oversight and quality control, as manufacturers can work more closely with suppliers and resolve issues more quickly. - Improved Collaboration and Communication
Proximity plays a critical role in fostering effective communication and collaboration between manufacturers and suppliers. Time zone differences and language barriers can complicate coordination with offshore partners, leading to delays in decision-making and misunderstandings about production specifications.
Nearshoring eliminates many of these challenges. With manufacturing facilities located nearby, companies can more easily engage in face-to-face meetings, conduct site visits, and ensure that their quality standards are met. This is particularly important for industries that require high levels of precision, such as aerospace or defense, where even small production errors can have significant consequences.
Windings Inc.: Nearshoring in Action
Windings Inc., a leader in engineered electromagnetic solutions, has embraced nearshoring as a key part of its growth strategy. The company’s recent acquisition of a manufacturing facility in Baja California, Mexico, highlights the advantages of nearshoring for industries that demand precision engineering and high performance.
By expanding into Mexico, Windings Inc. has positioned itself to better serve its customers in the aerospace, defense, and energy sectors. The Baja California facility provides Windings with greater flexibility to meet the varying production demands of its clients, offering both high-volume manufacturing and custom solutions for critical applications.
How Nearshoring Benefits Windings Inc.’s Customers
Incorporating nearshoring into your company’s operations can offer similar benefits—whether it’s shorter lead times, cost savings, or improved supply chain resilience. For industries that require a high level of precision and reliability, nearshoring is more than just a trend; it’s a strategic move toward long-term success.
- Increased Manufacturing Capacity
Windings Inc.’s acquisition of the Baja California facility allows the company to expand its manufacturing capacity while keeping production closer to its North American clients. This nearshoring move reduces the time required to deliver key components, such as custom electric motors, rotors, and stators, and enhances the company’s ability to respond to customer needs quickly and efficiently.
For example, aerospace and defense clients often require rapid prototyping and production runs to meet the tight deadlines associated with government contracts. By leveraging nearshoring, Windings can fulfill these orders without the extended lead times associated with overseas production. - Improved Supply Chain Flexibility
In addition to increasing capacity, nearshoring provides Windings Inc. with greater flexibility in its supply chain operations. The Baja California plant allows the company to better manage production schedules, adjust output to meet changing customer demands, and quickly resolve any supply chain issues that arise.
Moreover, by having a nearshore facility, Windings can implement a dual sourcing strategy, where it produces components both in the U.S. and Mexico. This approach reduces the risk of disruptions by providing multiple production locations, ensuring that customers continue to receive their products even if one facility experiences an unexpected delay. - Cost-Effective Production for High-Volume Manufacturing
For customers with high-volume production needs, nearshoring offers significant cost advantages. By shifting production to Mexico, where labor costs are lower than in the U.S. but closer and more predictable than in offshore locations, Windings can offer competitive pricing without sacrificing quality or delivery speed.
This cost-effective production is particularly valuable for industries like automotive and energy, where large-scale production is necessary to maintain market competitiveness. Nearshoring allows Windings to meet these demands while still maintaining the precision and reliability that its customers expect.
How Nearshoring Fits Into a Broader Manufacturing Strategy
While nearshoring offers numerous benefits, it is most effective when combined with other strategies, such as dual sourcing. Dual sourcing involves sourcing materials or manufacturing from two different locations or suppliers, providing a backup in case one supply chain is disrupted. By combining nearshoring with dual sourcing, companies can build even greater resilience into their operations, ensuring that production continues smoothly even in the face of unforeseen challenges.
For instance, Windings Inc.’s dual sourcing strategy includes maintaining its original facility in New Ulm, Minnesota, while leveraging the nearshoring advantages of its Baja California plant. This allows the company to spread production across two regions, minimizing the risks of supply chain disruptions while optimizing cost and delivery times.
Nearshoring as a Competitive Advantage
In a world where supply chains are increasingly vulnerable to disruptions, nearshoring has emerged as a powerful strategy for manufacturers seeking to enhance agility, reduce costs, and improve responsiveness. By bringing production closer to home, companies can better manage their supply chains, ensure timely delivery, and remain competitive in fast-paced industries.
Windings Inc.’s expansion into Baja California is a prime example of how nearshoring can be successfully integrated into a company’s broader manufacturing strategy. As more businesses recognize the benefits of nearshoring, we can expect this trend to continue reshaping the manufacturing landscape, providing greater stability and flexibility for industries that rely on precision-engineered components.
Incorporating nearshoring into your company’s operations can offer similar benefits—whether it’s shorter lead times, cost savings, or improved supply chain resilience. For industries that require a high level of precision and reliability, nearshoring is more than just a trend; it’s a strategic move toward long-term success.
For more information on how Windings can help you with your motor design and manufacturing needs, visit Windings Inc. or contact their team of experts directly.