Laser Welding in Electromagnetics: Revolutionizing High-Performance Motors
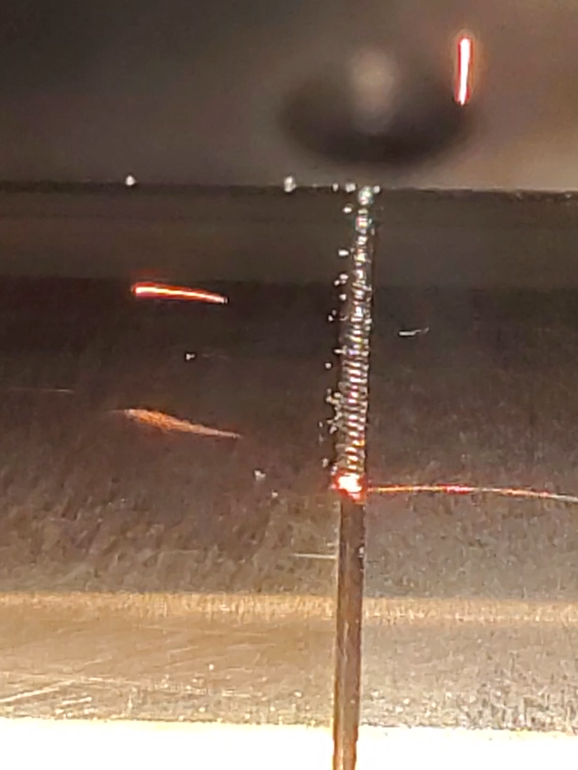
Introduction
Laser welding has emerged as a groundbreaking technology in the field of electromagnetics, particularly in the manufacturing of high-performance electric motors. This technique offers precision, strength, and efficiency, making it an ideal solution for assembling critical components in aerospace, defense, automotive, and clean energy applications. In this blog post, we will explore the principles of laser welding, its benefits in electromagnetics, and its impact on the industry.
Understanding Laser Welding
Laser welding utilizes a focused beam of light to melt and join materials together. The process involves directing a high-intensity laser beam onto the materials’ surfaces, causing them to melt and fuse upon cooling. This method offers several advantages over traditional welding techniques, including minimal heat-affected zones, reduced distortion, and the ability to weld complex geometries with high precision.
Applications in Electromagnetics
Laser welding is particularly beneficial in the production of electric motors, generators, and related components such as rotors, stators, and lamination stacks. Here are some key applications:
- Rotor Assembly: Laser welding is used to join rotor components, ensuring high strength and reliability. This is crucial for motors operating at high speeds and under extreme conditions, such as in aerospace and automotive applications.
- Stator Manufacturing: In stator production, laser welding allows for precise joining of thin lamination stacks, which are essential for reducing eddy current losses and improving motor efficiency.
- Magnet Retention: Laser welding provides a robust solution for securing magnets in place, particularly in high-speed applications where centrifugal forces can dislodge traditional adhesive bonds​​​​.
- Housing and Enclosures: The precision of laser welding is ideal for assembling motor housings and enclosures, ensuring tight seals and robust mechanical integrity.
Benefits of Laser Welding in Electromagnetics
The adoption of laser welding in electromagnetics brings numerous benefits that enhance the performance, reliability, and longevity of electric motors and other components:
- Precision and Accuracy: Laser welding offers unparalleled precision, allowing for the creation of complex and intricate designs. This is essential in the production of components that require tight tolerances and exact specifications.
- Strength and Durability: The welds produced by laser welding are exceptionally strong and durable. This is particularly important in high-stress applications where components must withstand significant mechanical and thermal loads.
- Minimal Heat-Affected Zone: One of the key advantages of laser welding is its ability to create strong joints with minimal heat-affected zones. This reduces the risk of thermal distortion and maintains the integrity of the materials being joined.
- Speed and Efficiency: Laser welding is a fast and efficient process, reducing production times and costs. This is crucial in industries where time-to-market is a critical factor.
- Flexibility: Laser welding can be used on a wide range of materials, including metals and alloys commonly used in electromagnetics, such as copper, aluminum, and various steels. This versatility makes it an ideal choice for diverse applications.
Industry Standards
- ISO 9001 and ISO/TS 16949: ISO 9001 sets the criteria for a quality management system and is used by organizations to ensure they can consistently provide products that meet customer and regulatory requirements. For the automotive industry, ISO/TS 16949 is an extension of ISO 9001, focusing on the development of a quality management system that provides for continual improvement, emphasizing defect prevention and the reduction of variation and waste.
- AS9100: This standard is specific to the aerospace industry and includes all the requirements of ISO 9001 along with additional requirements for aerospace and defense. AS9100 ensures that products meet stringent safety and reliability standards, making it critical for laser welding processes used in manufacturing aerospace components.
- IEC Standards: The International Electrotechnical Commission (IEC) sets standards for all electrical, electronic, and related technologies. IEC standards relevant to laser welding in electromagnetics include IEC 60825 for laser safety and IEC 61340 for electrostatic discharge control, ensuring safe and effective welding processes.
Regulatory Compliance
- Occupational Safety and Health Administration (OSHA): OSHA regulations ensure safe and healthful working conditions for employees. For laser welding operations, compliance with OSHA standards involves proper training, safety equipment, and protocols to protect workers from laser hazards.
- Environmental Protection Agency (EPA): The EPA regulates the environmental impact of manufacturing processes. Laser welding operations must comply with EPA regulations regarding emissions, waste management, and the use of hazardous materials to minimize environmental impact.
- Federal Aviation Administration (FAA): For components used in the aerospace sector, compliance with FAA regulations is essential. The FAA sets rigorous standards for the safety, performance, and reliability of aircraft components, including those manufactured using laser welding.
Quality Assurance and Testing
- Non-Destructive Testing (NDT): NDT methods such as ultrasonic testing, X-ray inspection, and dye penetrant testing are used to evaluate the integrity of welds without damaging the components. These tests ensure that laser welds meet the required quality standards and are free from defects that could compromise performance.
- Destructive Testing: Destructive testing methods, including tensile testing, hardness testing, and metallographic examination, involve subjecting welded components to stress or breaking them to evaluate their mechanical properties and weld quality. This type of testing helps verify that the welding process produces reliable and durable joints.
- Process Validation: Validation of the laser welding process involves documenting and proving that the process consistently produces welds that meet all specified quality and performance criteria. This includes process qualification, routine monitoring, and periodic revalidation to ensure ongoing compliance with industry standards.
Continuous Improvement
- Lean Manufacturing: Adopting lean manufacturing principles helps optimize laser welding processes by eliminating waste, improving efficiency, and enhancing quality. Continuous improvement initiatives focus on reducing cycle times, minimizing defects, and maximizing value to customers.
- Six Sigma: Six Sigma methodologies use data-driven approaches to improve process quality by identifying and eliminating defects. Implementing Six Sigma in laser welding operations involves rigorous analysis, process optimization, and control to achieve high-quality standards and customer satisfaction.
Challenges and Future Directions
Despite its numerous advantages, laser welding also presents some challenges that need to be addressed:
- Equipment Costs: The initial investment in laser welding equipment can be high. However, the long-term benefits in terms of precision, efficiency, and reduced production costs often justify the expense.
- Technical Expertise: Laser welding requires specialized knowledge and skills. Manufacturers need to invest in training and development to ensure their workforce can effectively utilize this technology.
- Material Considerations: Different materials have varying responses to laser welding. Manufacturers must carefully select appropriate materials and optimize welding parameters to achieve the desired results.
Looking ahead, advancements in laser welding technology are expected to further enhance its capabilities and applications. Developments in laser sources, such as fiber lasers and diode lasers, promise to increase efficiency, precision, and flexibility. Additionally, integration with automated and robotic systems will further streamline production processes and improve overall productivity.
Conclusion
Laser welding is revolutionizing the field of electromagnetics, offering unmatched precision, strength, and efficiency in the production of high-performance electric motors and components. Its applications in aerospace, automotive, and clean energy sectors underscore its versatility and impact on modern manufacturing. As technology continues to advance, laser welding will play an increasingly vital role in driving innovation and enhancing the performance of electromagnetic solutions.
For more information on how laser welding can benefit your applications, please contact Windings Inc. We specialize in engineered electromagnetic solutions and are committed to providing cutting-edge technologies to meet the demands of your industry.
For further information, please contact us!
Windings Inc.
1-800-795-8533
sales@www.windings.com
References
- Windings Inc. “Halbach Rotors for Advanced Air Mobility.” 2023.
- Windings Inc. “Magnet Retention for Mission Critical Applications.” 2019.
- Windings Inc. “Comparison of Different Permanent Magnet Arrangements of BLDC Motors.” 2023.
- Windings Inc. “Magnet Retention for Mission Critical Motor Applications.” 2020.