Environmental Chamber Testing: Ensuring Reliability in Extreme Conditions
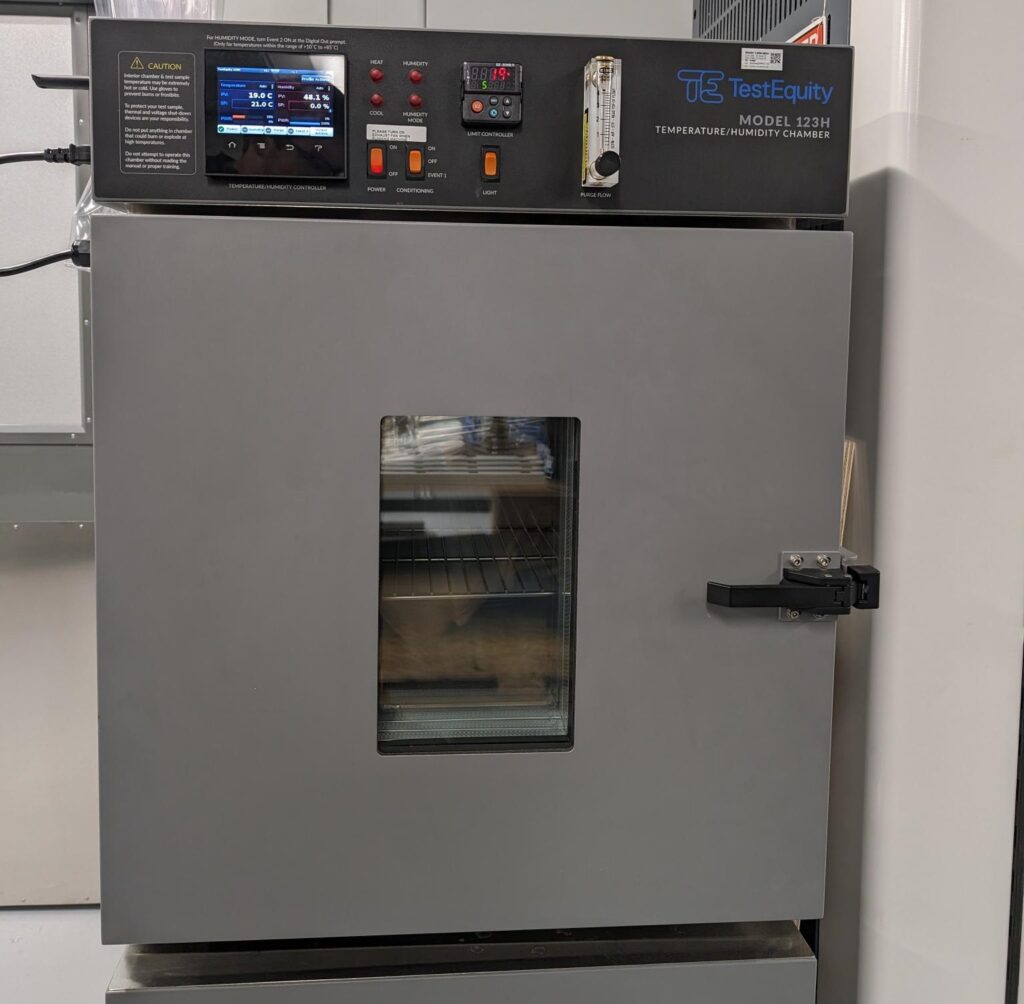
In industries where the performance of electromagnetic solutions like custom electric motors, generators, and related components is critical, environmental chamber testing is indispensable. This testing process involves exposing products to various simulated environmental conditions to ensure they can withstand real-world applications. Windings, Inc., a leader in providing engineered electromagnetic solutions, recognizes the importance of rigorous environmental testing to guarantee the reliability and longevity of its products across industries such as aerospace, defense, advanced air mobility, and energy.
The Critical Role of Environmental Chamber Testing
Environmental chamber testing is essential in industries where equipment operates under extreme conditions, including high and low temperatures, humidity, thermal shock, altitude, vibration, and corrosive atmospheres. The primary goal is to ensure that products can maintain their performance, reliability, and safety standards when exposed to such conditions.
- Temperature Testing:
- High-Temperature Testing: Equipment exposed to high temperatures must demonstrate the ability to operate without degradation. High temperatures can affect the magnetic properties of components like motors and rotors, leading to potential failures in critical applications. This is particularly important for applications in aerospace and defense, where components might face elevated temperatures during operation. For instance, electric motors used in downhole oil and gas applications must withstand temperatures exceeding 200°C while maintaining optimal performance.
- Low-Temperature Testing: Similarly, low-temperature testing ensures that components can start and function correctly in cold environments, such as those encountered in space or high-altitude applications. In advanced air mobility (AAM), where components might be exposed to sub-zero temperatures at high altitudes, low-temperature testing is crucial to ensure that systems remain operational during all flight phases.
- Humidity and Corrosion Testing:
- Humidity Testing: Many environments, particularly in energy and oil & gas sectors, have high humidity levels. Humidity testing checks for moisture ingress that could cause electrical shorts, corrosion, or material degradation. For instance, electric motors used in offshore drilling must be able to resist the corrosive effects of saltwater, which can cause rust and reduce the lifespan of the equipment.
- Salt Spray Testing: In marine or coastal environments, salt spray testing is vital to ensure that materials resist corrosion over time. Corrosion can lead to failure in critical components, especially in environments where maintenance opportunities are limited. For example, motors operating in subsea conditions must maintain their integrity despite constant exposure to saltwater.
- Thermal Shock Testing:
- Rapid Temperature Changes: Products may undergo rapid temperature fluctuations, particularly during high-speed operations or sudden environmental changes. Thermal shock testing ensures that components can survive these transitions without structural damage or performance loss. For instance, in defense applications, where equipment may be rapidly transported between different climates, thermal shock testing ensures that all components remain functional regardless of sudden temperature shifts.
- Vibration and Shock Testing:
- Mechanical Integrity: Vibration and shock testing are critical in environments with significant mechanical stresses, such as aerospace or automotive applications. This testing ensures that components like motors and rotors can withstand operational vibrations and mechanical shocks without failure. High-speed electric motors used in advanced air mobility must resist intense vibrations during takeoff and landing, ensuring the safety and reliability of the entire system.
- Altitude Testing:
- High-Altitude Conditions: For aerospace applications, altitude testing simulates the low-pressure environments encountered at high altitudes. This testing is crucial for ensuring that components function correctly in reduced atmospheric pressure, which can affect cooling and electrical performance. For example, components used in satellite systems must operate flawlessly at high altitudes, where the lack of atmosphere can lead to overheating if not properly tested.
- Ingress Protection (IP) Testing:
- Dust and Water Resistance: IP testing ensures that components can resist dust and water ingress, which is crucial in environments like oil and gas exploration where equipment is often exposed to harsh conditions. In these settings, any breach could lead to catastrophic failures, making IP testing a standard procedure for ensuring equipment longevity and reliability.
Methods and Technologies in Environmental Chamber Testing
Windings, Inc. employs advanced environmental chamber testing methodologies to simulate the diverse and extreme conditions its products may encounter. This process involves several key technologies and techniques:
- Controlled Environment Chambers: Windings uses state-of-the-art environmental chambers that can precisely control temperature, humidity, and other environmental factors. These chambers simulate conditions ranging from extreme heat and cold to rapid temperature changes, ensuring comprehensive testing of all product parameters. For example, custom electric motors designed for use in the defense sector are rigorously tested in these chambers to ensure they meet the stringent performance standards required in combat scenarios.
- Multi-Environment Testing: Testing often combines multiple environmental factors simultaneously, such as high temperature and humidity or vibration and thermal cycling. This approach ensures that products can withstand the complex, real-world conditions they will face in the field. For instance, a motor used in advanced air mobility might be tested under conditions that simulate the combined effects of altitude, temperature variations, and vibrations experienced during flight.
- Advanced Monitoring Systems: During testing, advanced sensors and monitoring systems are used to gather data on product performance in real-time. This data includes temperature, humidity levels, mechanical stress, and electrical performance, allowing engineers to assess how the product reacts under different conditions. For instance, in oil and gas applications, continuous monitoring during high-pressure and high-temperature tests provides critical insights into how components like rotors and stators will perform in extreme downhole environments.
- Accelerated Life Testing (ALT): ALT involves subjecting components to extreme conditions beyond their normal operating range to identify potential failure points. This method helps predict the product’s lifespan and ensures that it meets the durability requirements of critical applications. For example, ALT might be used to simulate several years of operation in a high-vibration environment, compressing this experience into a much shorter test period to assess the long-term reliability of a motor used in aerospace applications.
Applications of Environmental Chamber Testing in Electromagnetic Solutions
For Windings, Inc., environmental chamber testing is a critical step in the development and production of electromagnetic solutions for its key markets. Here’s how it applies across different sectors:
- Aerospace and Defense:
- Extreme Temperature and Altitude: Aerospace components must operate in a wide range of temperatures and altitudes. Environmental chamber testing ensures that motors, generators, and other components can handle the thermal and pressure variations encountered during flight and space missions. For example, satellite motors must be able to function reliably in the vacuum of space, where temperatures can fluctuate drastically.
- Vibration Resistance: Defense equipment often operates in environments subject to intense vibrations, such as in vehicles or aircraft. Testing for vibration resistance ensures that these components will not fail during critical operations, maintaining mission success and safety.
- Advanced Air Mobility (AAM):
- Vibration and Shock Resistance: For AAM applications, components must endure high levels of vibration and shock during takeoff, flight, and landing. Vibration testing is essential to verify that these components remain reliable under such conditions. For instance, electric motors used in AAM must maintain their performance despite the constant vibrations encountered during high-speed flight.
- Temperature Extremes: AAM vehicles may experience rapid changes in temperature, especially during high-altitude flight. Environmental testing ensures that all components can withstand these changes without performance degradation.
- Energy Sector:
- Corrosion Resistance: In the energy sector, particularly in oil and gas exploration, components are exposed to corrosive environments. Salt spray and humidity testing ensure that these components resist corrosion and maintain functionality over time. For instance, downhole motors used in drilling must resist corrosion from saltwater and other chemicals to avoid failures that could lead to costly downtime.
- High-Pressure Testing: Components used in deep-sea oil exploration are subject to extreme pressures. Environmental chamber testing simulates these pressures to ensure that motors, seals, and other critical components can withstand the intense conditions without failure.
- Automotive:
- Thermal Cycling and Humidity: Automotive components, especially those used in electric vehicles, must withstand thermal cycling and high humidity levels. Environmental testing ensures that these components can handle the thermal stresses and moisture encountered in different climates. For instance, electric vehicle motors are tested to ensure they can operate efficiently in both hot desert environments and cold, humid conditions without losing performance.
- Vibration Testing: Automotive applications often involve significant vibrations, especially in high-performance or off-road vehicles. Testing for vibration resistance ensures that components like motors and sensors will continue to function reliably, even in rough driving conditions.
Challenges and Future Directions
Environmental chamber testing is not without its challenges. The increasing complexity of modern electromagnetic solutions, coupled with the need for higher performance and reliability, demands continuous advancements in testing methodologies.
- Complex Test Simulations:
- Simulating real-world conditions with high fidelity requires sophisticated testing equipment and methodologies. As products become more advanced, the complexity of these simulations must increase accordingly. For example, testing for aerospace applications might involve simulating the exact conditions of a mission, including launch, space environment, and re-entry, all within a controlled chamber.
- Data Integration and Analysis:
- The large volumes of data generated during testing require advanced analytics to interpret. Integrating this data with product development processes helps engineers refine designs and improve performance. For instance, data collected from vibration and thermal cycling tests can be used to optimize the design of a rotor, ensuring it meets the required performance standards while minimizing material costs.
- Sustainability in Testing:
- As environmental concerns grow, there is increasing pressure to make testing processes more sustainable. This includes reducing the energy consumption of testing facilities and minimizing the environmental impact of testing procedures. For instance, using more energy-efficient chambers and recycling materials used in testing can reduce the carbon footprint of the testing process.
- Green Testing Initiatives: Some industries are exploring the use of renewable energy sources to power testing facilities, thereby reducing their reliance on fossil fuels. This approach not only supports sustainability goals but also aligns with broader industry trends towards greener practices.
- Miniaturization and Precision:
- As components become smaller and more integrated, testing processes must adapt to these changes. Miniaturized components require highly precise testing environments to ensure that even the smallest defects are identified and addressed. This is particularly important in industries like advanced air mobility and aerospace, where even minor flaws can lead to significant failures.
Conclusion
Environmental chamber testing is a cornerstone of ensuring the reliability and performance of electromagnetic solutions across various industries. For Windings, Inc., it is an integral part of the product development process, ensuring that its products meet the rigorous demands of aerospace, defense, advanced air mobility, energy, and automotive applications. As testing technologies evolve, they will continue to play a crucial role in advancing the capabilities and reliability of electromagnetic solutions in even the most extreme environments.
By embracing advanced testing methodologies and continuously refining their processes, Windings, Inc. is well-positioned to lead in the development of highly reliable, durable, and efficient electromagnetic components that meet the needs of the most demanding applications. The future of environmental chamber testing will likely involve even more sophisticated simulations, greater integration with digital twins, and a stronger emphasis on sustainability, ensuring that Windings remains at the forefront of innovation in this critical field.
For more information on our prototyping services and how we can help with your next project, please contact us at sales@www.windings.com or visit our website at www.windings.com.