Electric Motors in Harsh Environments: Engineering for Extreme Conditions
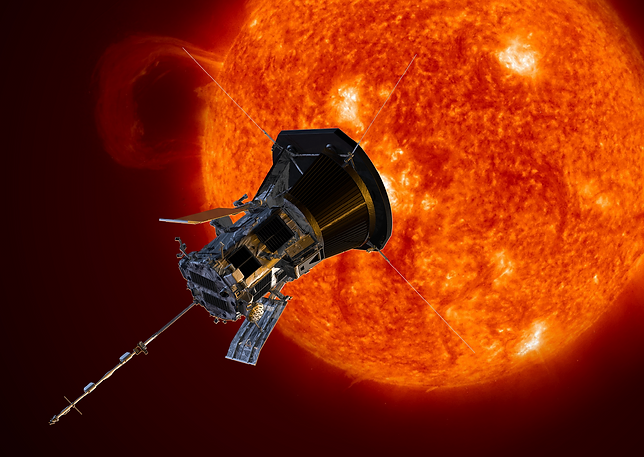
Electric motors are the backbone of numerous industrial applications, powering everything from manufacturing equipment to oil and gas extraction tools. When these motors are deployed in harsh environments—characterized by extreme temperatures, high pressures, corrosive substances, and abrasive conditions—they face unique challenges that demand specialized engineering solutions. This blog post explores the requirements, design considerations, and innovations in electric motors that ensure reliable performance in the most demanding environments.
Understanding Harsh Environments
Harsh environments encompass a variety of conditions that can significantly impact the performance and longevity of electric motors. Key factors include:
- Extreme Temperatures: Both high and low temperatures can affect motor components. High temperatures can lead to insulation breakdown and bearing failures, while low temperatures can cause brittleness in materials.
- High Pressure: Found in applications such as deep-sea exploration and downhole drilling, high pressure can deform motor housings and affect seals and bearings.
- Corrosive Environments: Chemical industries, marine applications, and wastewater treatment facilities expose motors to corrosive substances that can degrade materials and lead to failures.
- Abrasive Conditions: Mining, construction, and certain manufacturing processes involve exposure to dust, sand, and other abrasive materials that can wear down motor components.
Key Challenges and Solutions
Extreme Temperatures
Challenges:
- High temperatures can degrade insulation materials, causing short circuits.
- Bearings and lubricants can fail due to thermal expansion.
- Low temperatures can make materials brittle and prone to cracking.
Solutions:
- High-Temperature Insulation: Using advanced insulation materials such as mica, fiberglass, and ceramic can enhance thermal stability. These materials maintain their properties at temperatures up to 250°C and beyond.
- Cooling Systems: Incorporating liquid cooling or air-cooling systems helps dissipate heat. For instance, closed-loop liquid cooling systems circulate coolant through the motor to absorb and transfer heat away from critical components.
- Low-Temperature Materials: Selecting materials with low brittleness at sub-zero temperatures, such as certain stainless steels and specialized polymers, ensures durability.
High Pressure
Challenges:
- High pressure can lead to deformation of motor housings and seals, compromising performance.
- Bearings may experience increased load, leading to premature wear.
Solutions:
- Robust Housing Design: Utilizing materials like Inconel, titanium, and high-strength stainless steel can withstand high pressures without deformation. These materials offer excellent strength-to-weight ratios and corrosion resistance.
- Pressure-Resistant Seals: Advanced seal designs, such as labyrinth seals and magnetic fluid seals, provide reliable performance under high-pressure conditions. These seals prevent the ingress of contaminants and retain lubricants within the motor.
- Enhanced Bearings: Bearings designed for high-pressure environments often use ceramic balls or specialized steel to resist deformation and wear. Lubricants with high viscosity indices also ensure consistent performance under varying pressure conditions.
Corrosive Environments
Challenges:
- Exposure to chemicals and saltwater can lead to corrosion of motor components.
- Corrosive environments can cause pitting, cracking, and material loss.
Solutions:
- Corrosion-Resistant Materials: Employing materials like Hastelloy, Monel, and various grades of stainless steel helps resist corrosion. These materials are particularly effective in marine and chemical processing environments.
- Protective Coatings: Applying coatings such as epoxy, polyurethane, and Teflon can shield motor surfaces from corrosive agents. These coatings form a barrier that prevents direct contact between the motor and the corrosive environment.
- Sealed Motor Designs: Sealing motors with hermetically sealed enclosures prevents the ingress of corrosive substances. Explosion-proof enclosures are also used in hazardous environments to contain any potential internal faults.
Abrasive Conditions
Challenges:
- Dust, sand, and other abrasive particles can cause wear and tear on motor components.
- Abrasive conditions can lead to overheating and reduced efficiency.
Solutions:
- Durable Materials: Using hardened steel, ceramics, and composite materials for critical components such as bearings and shafts increases resistance to wear and abrasion.
- Protective Enclosures: Designing motors with IP (Ingress Protection) ratings appropriate for the environment, such as IP66 or higher, ensures protection against dust and particle ingress. These enclosures also help prevent moisture and contaminants from entering the motor.
- Maintenance Practices: Implementing regular maintenance schedules, including cleaning and lubrication, can extend the life of motors in abrasive environments. Automated systems for continuous monitoring and maintenance further enhance reliability.
Technical Innovations and Future Trends
Advancements in materials science, manufacturing processes, and sensor technologies continue to push the boundaries of what electric motors can achieve in harsh environments.
- Advanced Composite Materials: The use of carbon fiber and other advanced composites in motor housings and components offers high strength, low weight, and excellent resistance to corrosion and wear. These materials are particularly useful in aerospace and subsea applications.
- Smart Monitoring Systems: The integration of IoT and smart sensors allows for real-time monitoring of motor performance. These systems can detect early signs of wear, overheating, or other issues, enabling predictive maintenance and reducing downtime.
- Additive Manufacturing: Also known as 3D printing, additive manufacturing enables the production of complex motor components with optimized designs for specific environments. This technology allows for rapid prototyping and customization, leading to better performance and reliability.
Real-World Applications
Electric motors designed for harsh environments are critical in various industries, including oil and gas, aerospace, marine, and mining.
Oil and Gas
In the oil and gas industry, electric motors are used in downhole drilling operations, where they must withstand high temperatures, pressures, and corrosive drilling fluids. For example, downhole motors use high-strength alloys like Inconel and titanium to endure extreme conditions and ensure reliable operation.
Aerospace
Electric motors in aerospace applications face challenges such as high vibration, extreme temperatures, and exposure to various atmospheric conditions. Materials like titanium and advanced composites, along with specialized coatings, are used to enhance durability and performance.
Marine
Marine environments expose electric motors to saltwater, which is highly corrosive. Motors used in this sector are typically made from stainless steel and are coated with protective layers to prevent corrosion. Sealed designs also ensure that the motors remain operational even in submerged conditions.
Mining
In mining, electric motors operate in dusty, abrasive conditions. To combat this, motors are designed with robust housings and use materials like hardened steel and ceramics. Regular maintenance and protective measures such as filtration systems help ensure long-term reliability.
Conclusion
Electric motors designed for harsh environments are crucial for the reliable operation of critical industrial applications. Through the use of advanced materials, innovative design techniques, and cutting-edge monitoring technologies, these motors can withstand the most extreme conditions. Windings Inc., with its extensive experience in engineered electromagnetic solutions, continues to lead the industry in providing high-performance motors tailored to the unique challenges of harsh environments.
For more information on our prototyping services and how we can help with your next project, please contact us at sales@www.windings.com or visit our website at www.windings.com.