Copper Rotor Brazing: A Critical Process in Motor Efficiency and Durability
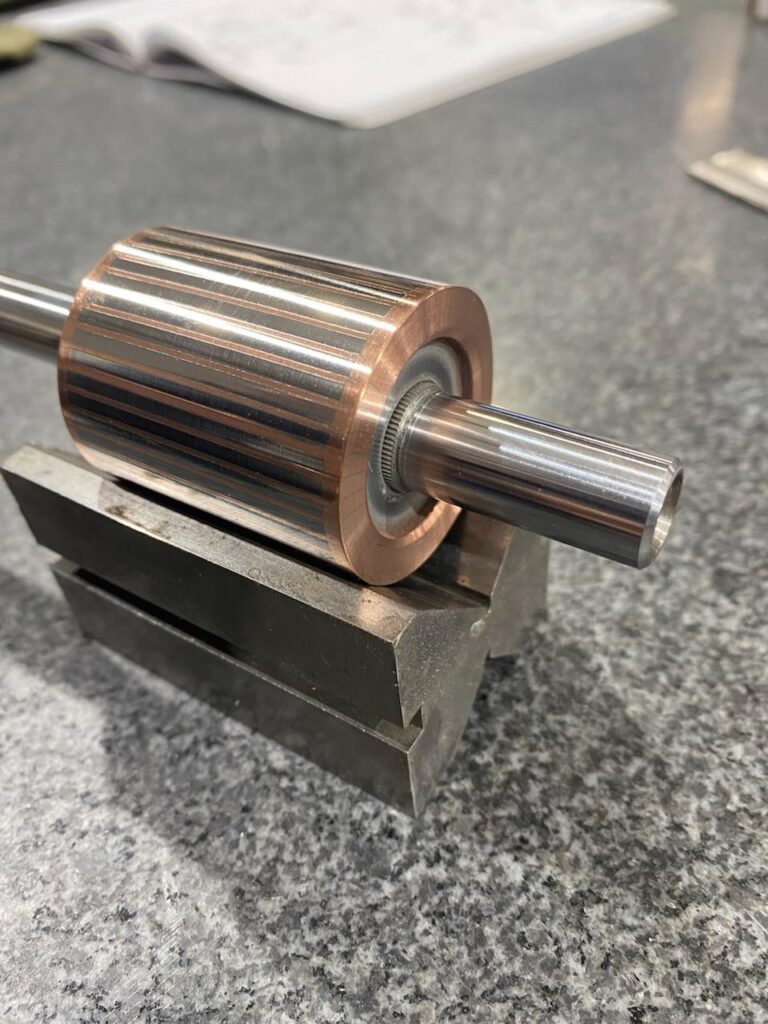
Rotor design is a critical factor in determining the overall efficiency, performance, and durability of the system. Copper rotor technology, especially in induction motors, has become increasingly popular due to its high electrical conductivity, which allows for improved motor efficiency. One of the key manufacturing processes in copper rotor production is brazing. This blog will explore the copper rotor brazing process, its importance, challenges, and its role in the manufacturing of high-performance electric motors.
The Importance of Copper in Electric Motors
Copper is a widely used material in electrical and electronic applications due to its excellent electrical conductivity, thermal conductivity, and mechanical properties. In electric motors, copper is primarily used for windings and in some cases for rotors. Aluminum is more commonly used for rotors because it is cheaper and easier to cast. However, copper offers a significant improvement in efficiency, particularly in applications requiring high performance, such as industrial motors, automotive applications, and electric vehicle propulsion systems.
The efficiency of an electric motor is largely determined by the reduction of losses, particularly I²R losses (resistive losses), which are related to the electrical resistance of the rotor and stator. Copper’s superior electrical conductivity (second only to silver among metals) reduces these losses, allowing motors to operate more efficiently compared to their aluminum counterparts. This reduction in energy loss is particularly important in high-duty cycle applications where even small improvements in efficiency can result in significant energy savings.
The Role of Brazing in Copper Rotor Manufacturing
Brazing is a metallurgical process that involves joining two or more metals by melting and flowing a filler metal into the joint. The filler metal has a lower melting point than the workpieces being joined, which means the base metals do not melt during the process. For copper rotors, brazing is used to join the copper conductors or bars to the end rings, creating a continuous electrical path and ensuring structural integrity.
The brazing process is essential for copper rotor production because of the complex shape and structure of the rotors. Unlike aluminum, which can be cast directly into the rotor’s slots during the die-casting process, copper requires brazing to connect the rotor bars to the end rings. This process must be carried out with high precision to ensure strong electrical conductivity and mechanical integrity, both of which are critical to the performance of the motor.
Brazing Process for Copper Rotors
The brazing process for copper rotors involves several critical steps, each of which must be carefully controlled to achieve the desired mechanical and electrical properties. Below is a detailed overview of the brazing process:
- Preparation of the Rotor Core
Before the brazing process can begin, the rotor core must be prepared. The rotor core consists of laminated steel sheets, which are stacked and assembled to form the body of the rotor. The copper bars are inserted into the slots in the rotor core, forming the conducting paths through which the current will flow.
Proper alignment of the copper bars is crucial to ensure that the brazing process results in a uniform and strong bond. Any misalignment can result in poor electrical contact or weak mechanical joints, both of which can negatively affect the performance and reliability of the motor. - Selection of Brazing Filler Material
The filler material used in brazing copper rotors is typically an alloy designed to bond well with copper while maintaining high electrical conductivity. Common filler materials for copper brazing include silver-based alloys, copper-phosphorus alloys, and brass. The choice of filler material depends on the specific application requirements, including the operating temperature of the motor, the mechanical stresses it will endure, and the desired electrical performance.
Silver-based brazing alloys are often preferred for their excellent flow characteristics and strong bond formation. However, they are more expensive than other filler metals, making them less desirable for cost-sensitive applications. Copper-phosphorus alloys are commonly used for lower-cost brazing but require careful control of the brazing atmosphere to prevent oxidation. - Application of Flux
Flux is a chemical cleaning agent used in brazing to prevent oxidation of the metal surfaces during heating. In the brazing process, flux is applied to the joint area before heating to remove any oxides and impurities, ensuring that the filler metal can flow and bond with the base metals.
The type of flux used depends on the base and filler metals. In copper rotor brazing, the flux must be capable of withstanding the high temperatures required to melt the filler metal, while also being easy to remove after the process is complete. Flux residue left on the rotor can lead to corrosion and reduce the long-term reliability of the motor. - Heating
The most common methods for heating in the copper rotor brazing process include induction heating, furnace brazing, and torch brazing. Induction heating is the most popular method due to its precise control over temperature and localized heating capabilities. In this method, the rotor assembly is placed within an induction coil, which generates a magnetic field. The resulting eddy currents in the copper components cause localized heating, melting the filler metal and allowing it to flow into the joint.
Furnace brazing is used for batch processing, where multiple rotor assemblies are brazed simultaneously in a controlled atmosphere furnace. This method is ideal for large-scale production, as it ensures uniform heating and minimizes the risk of oxidation. However, furnace brazing may require more complex fixturing and longer cycle times compared to induction brazing.
Torch brazing, while less common, is sometimes used for small-scale or repair applications. It involves manually heating the joint area with a gas flame, making it suitable for applications where precise control over the heating process is not as critical. - Cooling
After the filler metal has melted and flowed into the joint, the assembly is allowed to cool. The cooling process must be carefully controlled to prevent the formation of cracks or voids in the joint, which can compromise the mechanical strength and electrical conductivity of the rotor.
In some cases, forced cooling using air or water is employed to speed up the process. However, care must be taken to avoid thermal shock, which can occur if the cooling rate is too rapid. Thermal shock can lead to warping of the rotor or weakening of the brazed joints, which can affect the performance of the motor. - Cleaning
Once the brazing process is complete and the assembly has cooled, any remaining flux residue must be removed. This is typically done using chemical cleaning agents or abrasive methods. Flux residue can cause corrosion and degrade the performance of the motor over time, so thorough cleaning is essential. - Inspection and Testing
The final step in the brazing process is inspection and testing. The brazed joints are visually inspected for any defects, such as cracks, voids, or incomplete bonding. In some cases, non-destructive testing methods, such as X-ray inspection or ultrasonic testing, are used to ensure the integrity of the joints.
Electrical testing is also performed to ensure that the rotor meets the required performance specifications. This typically involves measuring the electrical resistance of the rotor bars and end rings to ensure that the brazing process has not introduced any unwanted resistance or discontinuities.
Challenges in Copper Rotor Brazing
While copper rotor brazing offers significant advantages in terms of motor performance and efficiency, it also presents several challenges:
- High Melting Point of Copper
One of the primary challenges in brazing copper rotors is the high melting point of copper (1085°C). This requires high temperatures during the brazing process, which can lead to thermal stress and distortion of the rotor components. Careful control of the heating and cooling process is essential to avoid damage to the rotor assembly. - Oxidation
Copper is highly susceptible to oxidation at elevated temperatures. Oxidation can prevent the filler metal from properly bonding to the copper surfaces, leading to weak joints and poor electrical conductivity. To mitigate this, brazing must be carried out in a controlled atmosphere, such as a vacuum or an inert gas environment, to prevent oxidation. - Thermal Expansion
Copper has a relatively high coefficient of thermal expansion, which means that it expands and contracts significantly with changes in temperature. This can create stresses in the brazed joints during the heating and cooling process, leading to the formation of cracks or voids. The brazing process must be carefully controlled to minimize these thermal stresses and ensure the integrity of the joints. - Flux Residue
The removal of flux residue after brazing is critical to ensure the long-term reliability of the motor. Residual flux can cause corrosion, particularly in high-temperature or high-humidity environments. Proper cleaning methods must be employed to remove all traces of flux from the rotor assembly.
Advantages of Copper Rotor Brazing
Despite the challenges, the brazing of copper rotors offers several key advantages that make it a preferred method for high-performance motor manufacturing:
- Increased Motor Efficiency
The use of copper rotors in electric motors significantly reduces resistive losses, improving overall motor efficiency. This is particularly important in high-duty cycle applications where energy savings can be substantial. - Improved Thermal Conductivity
Copper’s excellent thermal conductivity helps dissipate heat generated during motor operation, reducing the risk of overheating and extending the motor’s lifespan. - Higher Mechanical Strength
Brazed copper joints provide high mechanical strength, ensuring the durability of the rotor assembly under high mechanical and thermal stresses. This is critical for applications where the motor is subjected to high speeds, heavy loads, or extreme temperatures.
Conclusion
Copper rotor brazing is a critical process in the manufacturing of high-efficiency electric motors. By leveraging copper’s superior electrical and thermal properties, and using brazing to create strong, conductive joints, manufacturers can produce motors that deliver superior performance, reliability, and energy efficiency. Despite the challenges involved in brazing copper rotors, advancements in brazing techniques and materials continue to push the boundaries of what is possible in electric motor design, making copper rotor technology an increasingly viable solution for high-performance applications.
For more information on how Windings can help you with your motor design and manufacturing needs, visit Windings Inc. or contact their team of experts directly.