Complete Motors in Housing: A Comprehensive Exploration
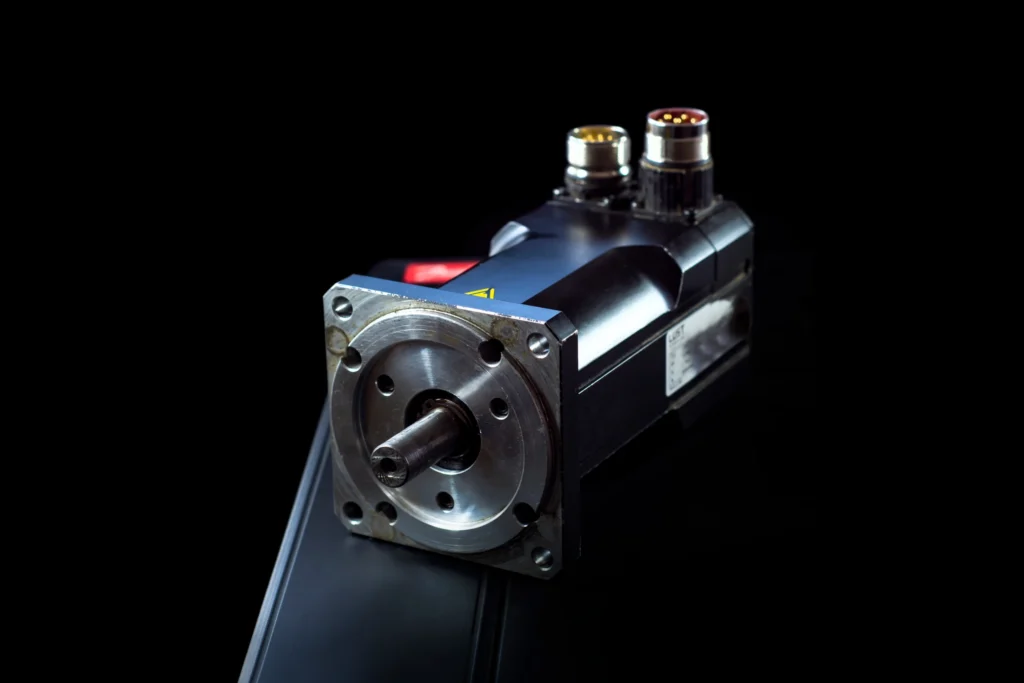
In the ever-evolving world of electric motor technology, the demand for robust, high-performance solutions has never been greater. From aerospace to automotive, industries across the board are seeking advanced motor designs that can deliver unparalleled efficiency, reliability, and durability in the harshest environments. One such innovation is the development of complete motors in housing—an all-encompassing approach that integrates the motor components within a protective casing. This design not only enhances the motor’s performance but also extends its operational life, making it a crucial element in various critical applications.
This blog post delves into the concept of complete motors in housing, exploring their design, advantages, applications, and the pivotal role Windings, Inc. plays in pushing the boundaries of this technology. Whether you’re an engineer looking for the latest advancements in motor design or a procurement specialist seeking reliable solutions for your next project, this comprehensive guide will provide valuable insights into why complete motors in housing are the future of electric motor technology.
Understanding Complete Motors in Housing
A complete motor in housing refers to an electric motor that is fully enclosed within a protective casing or housing. This design serves multiple critical functions:
- Protection from Environmental Factors: The housing acts as a shield, protecting the internal components from dust, moisture, chemicals, and other environmental hazards. This is particularly important in industries such as oil & gas, where motors are often exposed to harsh conditions that can lead to corrosion and wear.
- Structural Integrity and Durability: The housing provides essential structural support, ensuring that the motor components remain securely in place during operation, even under high stress, such as in high-speed or high-torque applications. This structural integrity is crucial in maintaining the motor’s performance and longevity.
- Thermal Management: Heat management is a key challenge in motor design. Complete motors in housing often include features like cooling fins or integrated liquid cooling channels that help dissipate heat, thus preventing overheating and maintaining optimal performance.
- Noise Reduction: The enclosed design of the motor housing also helps to dampen operational noise, making these motors ideal for applications where noise control is a significant concern, such as in urban environments or within machinery that operates in close proximity to personnel.
- Ease of Integration: Complete motors in housing are designed with ease of integration in mind. They come with standardized mounting points and connection interfaces, which simplify their incorporation into larger systems. This is particularly beneficial in industries like automotive and aerospace, where space and compatibility are critical considerations.
Key Design Considerations
Designing a complete motor in housing is a complex process that requires careful consideration of various factors, including the application environment, performance requirements, and material selection.
- Material Selection:
- Housing Material: The choice of housing material is critical for ensuring durability, weight management, and resistance to environmental factors. Common materials include stainless steel, aluminum, and specialized composites. Stainless steel offers excellent corrosion resistance, while aluminum provides a lighter alternative with good thermal conductivity. In certain high-performance applications, advanced composites may be used for their strength-to-weight ratio and specialized thermal properties.
- Magnet Retention: The magnets in the rotor are vital to the motor’s performance, especially in high-speed applications. To ensure these magnets stay securely in place, advanced retention methods such as carbon fiber roving or metal alloy sleeves are employed. Carbon fiber is favored for its high strength-to-weight ratio and low thermal expansion, making it ideal for high-speed motors where minimizing mass and thermal stress is crucial.
- Thermal Management:
- Cooling Mechanisms: Efficient thermal management is vital to prevent overheating, which can degrade performance and shorten the motor’s lifespan. Complete motors in housing typically employ either air-cooled or liquid-cooled systems. Air-cooled systems rely on airflow across the housing surface, while liquid-cooled systems use a coolant that circulates through integrated channels in the housing. The choice between these systems depends on the motor’s operational environment and performance requirements.
- Insulation Systems: In high-temperature environments, such as those found in oil & gas drilling, the motor’s insulation system must be capable of withstanding extreme heat while maintaining electrical integrity. Advanced insulation materials, capable of operating at temperatures exceeding 200°C, are often used to ensure reliability and longevity in such conditions.
- Sealing and Environmental Protection:
- Ingress Protection: In environments where motors are exposed to dust, moisture, and chemicals, the housing must provide a high level of ingress protection. This ensures that contaminants do not enter the motor, which could lead to performance degradation or failure. Motors used in marine or underwater applications, for example, require housings with high IP ratings to withstand prolonged exposure to water and salt.
- Pressure Resistance: In high-pressure environments, such as deep-sea exploration or downhole drilling, the motor housing must be capable of withstanding significant external pressures without deforming or failing. This requires the use of materials and designs that can maintain integrity under extreme pressure conditions.
- Performance Optimization:
- Efficiency: Achieving high efficiency is a primary goal in motor design, especially in applications where energy consumption directly impacts operational costs. Design considerations such as minimizing friction, optimizing the air gap between the rotor and stator, and selecting low-loss materials all contribute to higher efficiency. Precise manufacturing processes are also essential to achieving the tight tolerances required for optimal performance.
- Power Density: Power density, or the amount of power output per unit volume, is a critical factor in applications where space and weight are limited, such as in aerospace and automotive industries. Techniques such as using high-energy permanent magnets and advanced winding technologies are employed to maximize power density without increasing the motor’s size.
Applications of Complete Motors in Housing
Benefits of utilizing Windings to manufacture the complete motor & housing are deployed across a wide range of industries, each with unique requirements and challenges. Below are some of the key applications:
- Aerospace and Defense:
- High-Speed Applications: Aerospace applications often demand motors that operate at extremely high speeds, sometimes exceeding 100,000 rpm. These motors are used in electric turbochargers, energy recovery systems, and other high-performance systems where reliability at high rotational speeds is critical. The housing must be robust enough to handle the centrifugal forces and thermal loads associated with these speeds while maintaining precise mechanical tolerances.
- Mission-Critical Reliability: In defense applications, the reliability of motors can be a matter of life and death. These motors must perform flawlessly under extreme conditions, such as high shock, vibration, and temperature extremes, without requiring frequent maintenance or replacement. Windings, Inc. designs motors with these stringent requirements in mind, ensuring that they can withstand the harshest conditions.
- Automotive:
- Electric and Hybrid Vehicles: The automotive industry is rapidly moving towards electrification, with electric and hybrid vehicles becoming more prevalent. These vehicles require motors that are compact, efficient, and capable of delivering high power density. Complete motors in housing are ideal for these applications because they offer protection against environmental factors such as road debris, moisture, and temperature fluctuations, ensuring reliable performance over the vehicle’s lifespan.
- Advanced Air Mobility:
- The emerging field of advanced air mobility (AAM) presents new challenges and opportunities for electric motor technology. eVTOL (electric Vertical Take-Off and Landing) aircraft, for example, require lightweight, high-efficiency motors that can deliver the necessary power for vertical lift and sustained flight. The design and housing of these motors must balance the need for performance with stringent weight and safety requirements.
- Oil & Gas:
- Downhole Tooling: In the oil and gas industry, motors used in downhole tooling must operate in some of the harshest environments imaginable, including high pressure, high temperature, and exposure to corrosive fluids. Complete motors in housing are designed to withstand these extreme conditions, providing reliable power for tools used in drilling, measurement, and other critical operations. The housing must be capable of protecting the motor’s internal components while maintaining a compact form factor that can fit within the tight confines of a wellbore.
- Pumping and Drilling: Electric motors are increasingly being used to replace traditional hydraulic systems in oil and gas drilling and pumping operations. Electric motors offer better efficiency, more precise control, and lower maintenance requirements compared to hydraulics. The housing design is critical in these applications, as it must protect the motor from the harsh drilling environment while ensuring consistent performance under variable loads.
The Role of Windings, Inc. in Advancing Motor Housing Technology
For over 50 years, Windings, Inc. has been a leader in the development of complete motors in housing, providing engineered electromagnetic solutions for critical applications across multiple industries. Their expertise spans from design and testing to manufacturing and support, making them a trusted partner for companies that demand the highest levels of performance and reliability from their motors.
- Custom Solutions for Complex Applications: Windings, Inc. specializes in creating custom motor solutions tailored to the specific needs of their clients. Whether the challenge is extreme temperatures, high-pressure environments, or space constraints, Windings’ engineering team works closely with clients to develop motors that meet or exceed their expectations. This level of customization ensures that the motors are perfectly suited to the application, delivering optimal performance and reliability.
- Innovative Manufacturing Techniques: Windings utilizes advanced manufacturing techniques to ensure that each motor housing is crafted to the highest standards. This includes the use of precision machining, carbon fiber winding for magnet retention, and automated assembly processes that ensure consistency and accuracy across all production stages. These techniques not only enhance the motor’s performance but also ensure that it can withstand the rigors of its intended application.
- Focus on Reliability and Performance: Reliability is a hallmark of Windings’ products. The company’s motors are designed to excel in mission-critical applications, where failure is not an option. This includes ensuring that every component, from the rotor and stator to the housing and insulation, is optimized for longevity and performance under the most demanding conditions. Windings’ commitment to quality is reflected in their rigorous testing processes, which simulate real-world operating conditions to ensure that every motor performs as expected.
- Industry-Leading Expertise: With decades of experience in the field, Windings’ engineers bring a wealth of knowledge to every project. They are experts in the design and production of complete motors in housing, with a deep understanding of the challenges and requirements of different industries. Whether it’s selecting the right materials, optimizing thermal management systems, or integrating advanced features like magnet retention systems, Windings’ team is equipped to handle the most complex motor design challenges.
Conclusion
Complete motors in housing represent a significant advancement in electric motor technology, providing enhanced protection, reliability, and performance in a wide range of applications. As industries continue to push the boundaries of what is possible with electric motors, the demand for these robust, high-performance solutions will only grow.
Windings, Inc. stands as a leader in this field, offering custom-engineered motor solutions that meet the most stringent requirements. Whether for aerospace, automotive, or oil & gas applications, Windings’ expertise in designing and manufacturing complete motors in housing ensures that clients receive the highest quality products tailored to their specific needs.
For more information on how Windings can help you with your motor design and manufacturing needs, visit Windings Inc. or contact their team of experts directly.