OIL & GAS CASE STUDY
Home / Focus Industries / Downhole Motors for Oil and Gas Drilling / Advanced Air Mobility
CUSTOM ELECTRIC MOTOR FROM WINDINGS DELIVERS POWER, EFFICIENCY AND RELIABILITY IN HARSH DOWNHOLE ENVIRONMENT

CHALLENGE
Design an electric motor solution to drive a wireline hydraulic pump given the following constraints:
-
Output power = 5kW
-
Housing diameter less than 3.5″
-
Ambient temperatures up to 200°C
-
Capable of operating while submerged in hydraulic fluid
-
Life expectancy of at least 500 hours
-
Highest possible efficiency
SOLUTION
Custom 5kW, 8,000RPM permanent magnet motor in a stainless steel 3-1/8″ O.D. x 11″ long housing rated for 260°C operation while submerged in hydraulic fluid.
RESULTS
Relative to the induction motor it was replacing, the Windings permanent magnet motor provided:
-
50% reduction in motor package size, reducing tool string length by 11″
-
Over 90% increase in efficiency, almost doubling the productive time between battery swaps
-
750 hours of operation without failure (testing ongoing)
CUSTOM ELECTRIC MOTOR FROM WINDINGS DELIVERS POWER, EFFICIENCY AND RELIABILITY IN HARSH DOWNHOLE ENVIRONMENT
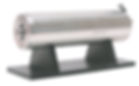
A design study conducted by Windings’ engineers revealed that the induction motor topology utilized by the manufacturer was not capable of meeting their goals for higher power density and high efficiency over the entire operating envelope. Because permanent magnet-based rotors do not require induction of a magnetic field, motors based on this topology have efficiencies greater than 90% over a wide speed / torque range and offer up to twice the power density of a comparable induction-based motor design. Therefore, a permanent magnet topology was selected as the basis of Windings’ recommended design.
Meeting the requirement for high reliability in an environment with an ambient temperature of 200°C proved a significantly greater challenge than the power density and efficiency requirements. At elevated temperatures the ability to dissipate heat generated by current flowing in the motor windings is diminished significantly. To prevent heat-induced breakdown of the winding varnish used for electrical insulation, the motor’s maximum current rating must be de-rated in proportion to the elevated ambient temperature, and since current is proportional to torque the motor’s power output must also be de-rated to avoid permanently damaging the motor.
The insulation system typically used in commercially available standard motors is rated for 155°C operation while only allowing full motor power output up to 40°C ambient. To meet the power density requirements in ambient temperatures up to 200°C, Windings’ engineers selected a proprietary magnet wire having an insulation system rated for 260°C, enough headroom to achieve full power at maximum ambient temperature without risk of motor damage. Similar material selection analysis was conducted for other critical components such as gaskets, seals and connector components to ensure the manufacturer’s motor life goal would be met.
The resulting motor from Windings provided 5kW of power at 8,000RPM while operating at 200°C ambient temperature. Efficiency was increased by over 90% relative the induction motor it was replacing, almost doubling the productive working time. And at 3-1/8″ in diameter and 11″ long, the overall package length was reduced by 2/3. Testing is still underway, but at time of writing the Windings motor had been operating without failure for more than 500 hours. Although the bearings will likely need replacement after 1,000 hours of operation due to contaminants inherent in the environment, it is anticipated that with minimal additional maintenance the motor will remain operational for at least 2,000 hours.
For more than 20 years, Windings has pioneered the development of electromagnetic solutions for critical upstream applications in the Oil & Gas industry. As a full-service provider, Windings is a leader in the design, test, manufacture and support of custom electric motors, alternators and related components engineered to survive and perform under the hostile conditions of downhole drilling and wireline tooling.